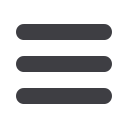
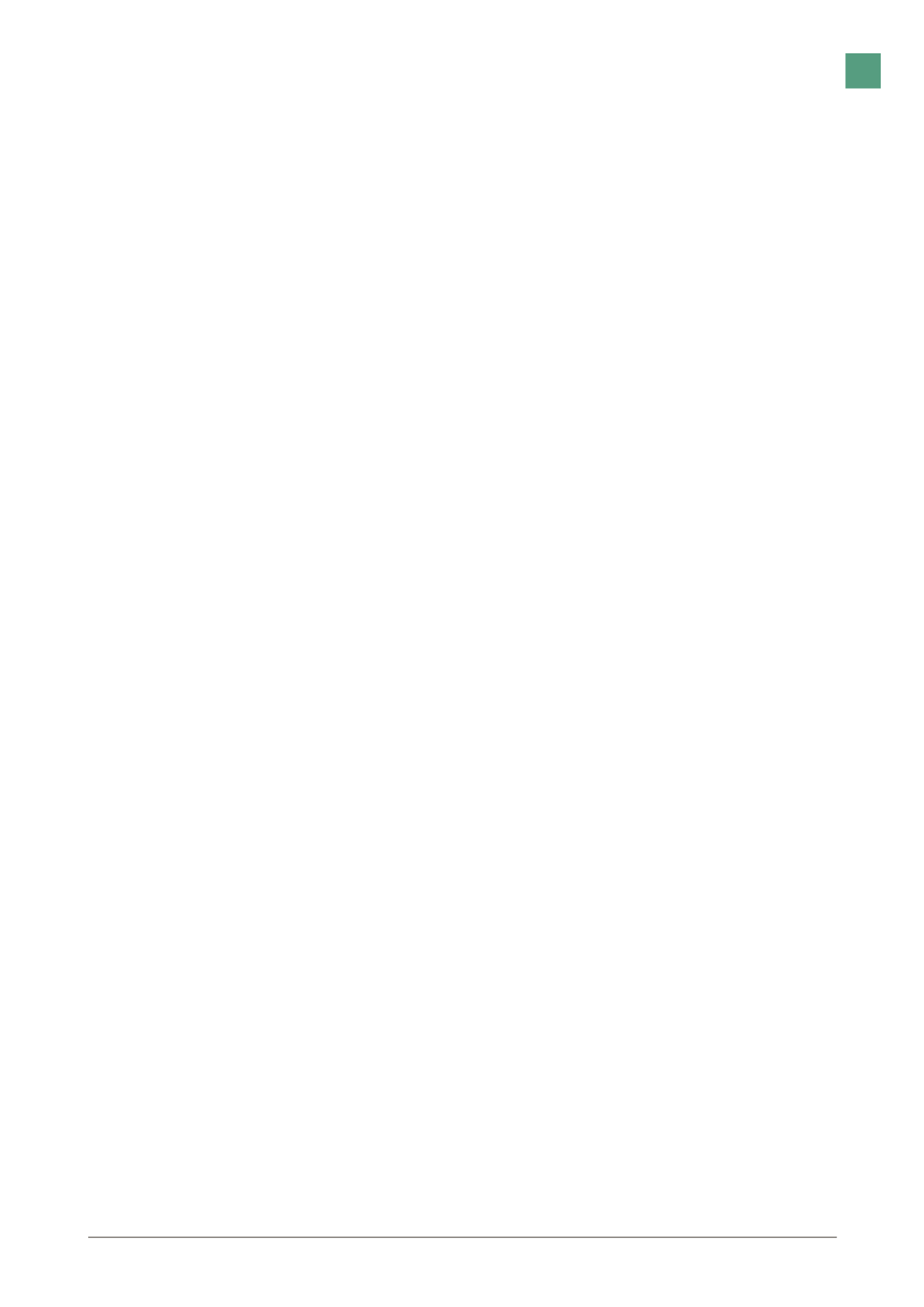
LISI 2016 FINANCIAL REPORT
99
56% of the LISI sites achieved the ambitious objective set for them,
namely to have a TF1 of less than 10.
Nevertheless, the LISI Group recorded 74 occupational illnesses
over all its sites, despite many efforts made in the implementation of
handling equipment and the wearing of hearing protection.
Although the TG0 severity rate (TG0) – which represents the number
of days lost as a result of workplace accidents per thousand hours
worked – improved compared with 2015, it remained at a relatively low
level, i.e. 0.276 days lost per thousand hours worked.
Each employee plays a major role in terms of prevention and LISI works
to involve all employees in this process.
1.5
I
TRAINING
LISI has made skills development through training one of the major
focuses of its Human Resources policy. It enables its staff to remain
at the highest skills level, on a market subject to rapid technological
changes and strong competition. LISI ensures that all employees,
regardless of their age or position, have access throughout their career
to the training courses necessary for the construction of their career
path and their adaptation to changes in the businesses.
In 2016, at least 258,000 training hours were completed, i.e. 1.45% of
the total hours worked during 2016. The internal and external training
budget across all LISI Group sites stood at €6.1 million in 2016,
equivalent to 1.6% of the Group’s payroll.
Hence, over 9,800 employees (81% of the Group’s workforce) have
attended training courses.
■■
To help the staff to have the level required by our businesses,
we are setting up appropriate and certification training programs,
focused on our strategic businesses: cold stamping, heat treatment,
machining, rolling, laminating, automatic control, surface treatment.
Hence, within the LISI AUTOMOTIVE division, nearly 5,900 hours
were dedicated to these career paths, and 42 CQPM/CQPI
qualifications were obtained in 2016.
■■
With 953 participants in training courses (33% more than in 2015),
the company university LISI Knowledge Institute (LKI)
was
confirmed not only as a pillar in the strategy for the development of
employee skills but also a major tool for the retention of talents and
the attraction of candidates with high potential.
The training offer is structured around three key topics:
–
–
management;
–
–
personal development;
–
–
training techniques for the businesses.
■■
2016
saw the continued deployment of the LISI Excellence
Achievement Program (LEAP) training
sessions, initiated in 2011.
LEAP is the LISI Group’s comprehensive participatory management
method aiming at operating excellence. Available in all the Group’s
plants (and also in many departments), it is based on an organization
on three levels (APG,APU, Site), problem-solving projects (PSM1/2/3),
continuous improvement tools (5S, 8D, SMED, Six Sigmas, etc.),
abundant and varied communications tools (standard visuals, films,
guides, etc.) and, above all, on an ambitious training program.
Since 2011, LISI has undertaken a wide program of training in the
LEAP fundamentals: the LEAP Basics training is now the prerequisite
for all new employees; and from 2015, training courses dedicated to
the Advanced LEAP tools have been organized, taking care to combine
learners from all divisions in the Group.
To support changes in the APU organization under the LEAP, in 2016,
the staff were able to take advantage of tailored training courses in
management, team building and training on the workstation.
■■
Internal training courses
were also developed within the group:
in technical areas and occupations (metallurgy, cold stamping,
material resistance, plastics and injection, procurement negotiation,
legal training, marking, turning, etc.), the training courses are run by
LISI employees who become involved to transmit their expertise
and their know-how.
■■
The Safety focus
remained a priority in 2016. Each site launched a
training program called SCP (Safety Culture Program). The aim of
this program is to address behavior-related causes of occupational
accidents by providing managers with the keys to understand
hazardous behaviors and giving them the levers to correct them.
This program also aims to develop a Safety Culture among
employees through the deployment of a structured and regular
communication campaign.
1.6
I
DIVERSITY AND EQUAL OPPORTUNITY/
EQUAL TREATMENT
Diversity is maintained by the managers who motivate men and
women with a variety of profiles and career paths.
Company agreements were signed to promote professional gender
equality. The main working focuses concern the recruitment,
compensation and organization of working hours.
Within the recruitment context, we are attempting to use objective and
professional criteria in sorting the resumés received, from applicants
met or promotions to be made.
Furthermore, with regard to work in favor of disabled employees, the
objective is above all to integrate disabled employees into the teams,
by adapting their workstation if required. Mission succeeded on the
Cejc, Fuenlabrada, Saint-Brieuc or Caen sites.
Corporate social responsibility
6