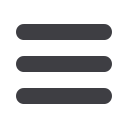
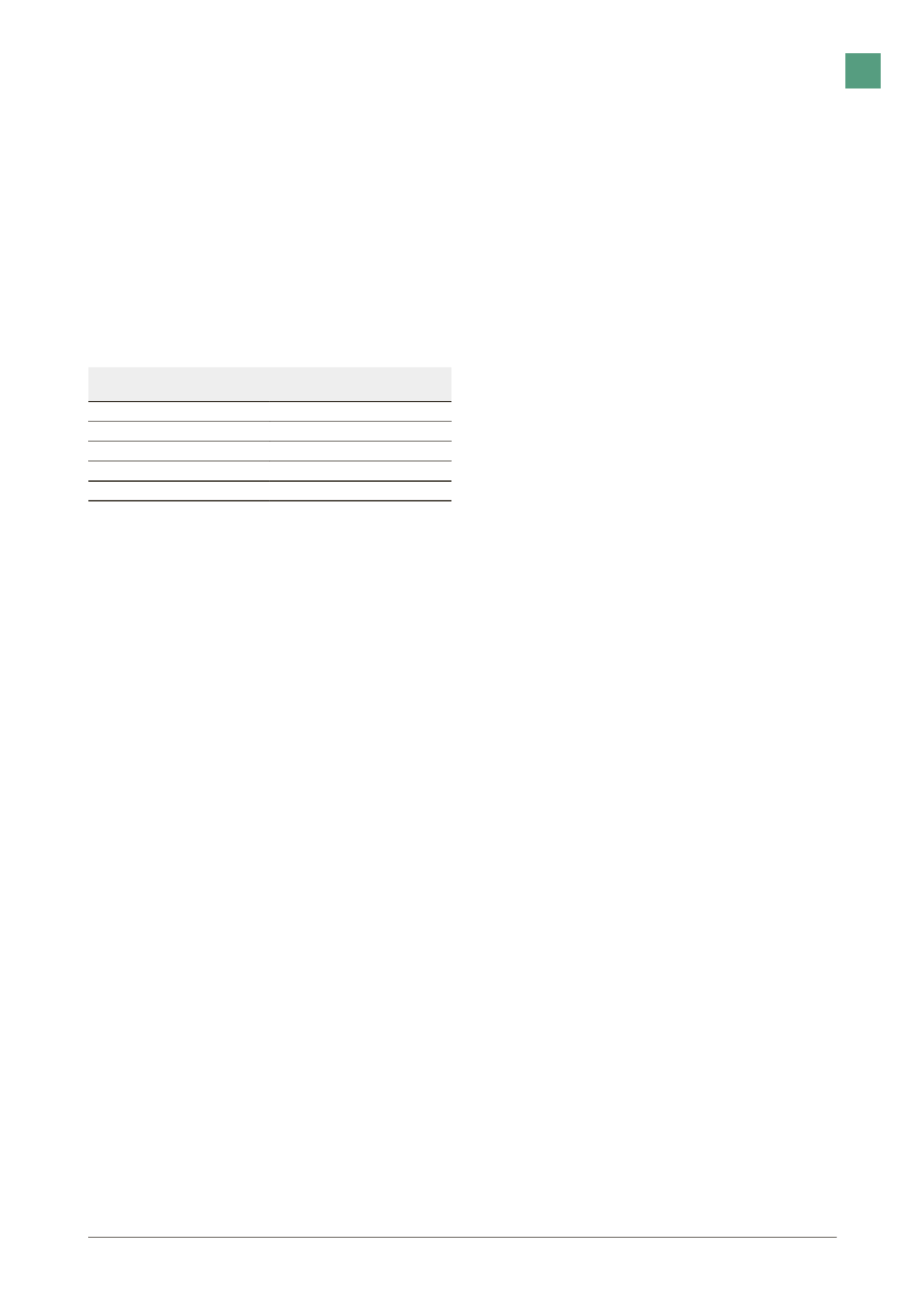
LISI 2016 FINANCIAL REPORT
101
Notable investments include:
–
–
the improvement of waste-water discharges – Bar sur Aube –
€619,000;
–
–
oil filtration system – Saint-Ouen l’Aumône – €316,000.
2.1.4
I
The amount of provisions and guarantees
for environmental risks, provided that such disclosure
is not likely to cause serious harm to the Company
in an ongoing dispute
The consolidated amount of HSE risk provisions by division is as
follows:
Division
Amount of HSE provisions 2016
LISI AEROSPACE
€6,768,000
LISI AUTOMOTIVE
€340,000
LISI MEDICAL
€212,000
LISI
€1,376,000
TOTAL
€8,696,000
2.2
I
POLLUTION AND WASTE MANAGEMENT
2.2.1
I
Measures to prevent, reduce or repair emissions
to air, water and soil that seriously affect the environment
LISI closely monitors the direct impact its direct production sites may
have on the environment. The best technology is sought to reduce the
environmental footprint and to anticipate potential regulations.
The surface treatment lines generally benefit from these technologies
because their atmospheric emissions and wastewater discharges may
affect the surrounding environment if they are not controlled.
All the industrial sites in the LISI Group were certified to ISO 14001,
apart from the Business Group Forging & Casting acquired in 2014.
Therefore, a detailed analysis of the environmental impact, the
so-called “Environmental Analysis”, is carried out by each of them. To
maintain this certification, the sites must implement actions to reduce
the environmental footprint of those activities or tasks identified as
the most significant.
2.2.2
I
Measures to prevent, recycle, and eliminate waste
The waste production indicator is, for 2016, 57.29 kg of waste for
€1,000 of added value.
Moreover, the portion of waste sorted is still very high, 95.7%, increasing
compared with 2015. The remaining portion concerns domestic waste
generated by production-related activities (toilets, cafeterias, etc.).
The LISI AUTOMOTIVE division is the largest producer of waste. This
is due to the large quantities of materials used and produced. But it is
also the division that best sorts its waste, with 96.7% of waste sorted.
LISI AEROSPACE sorts 94.5% of its waste.
The LISI MEDICAL division, in turn, only accounts for 1.3% of the waste
produced.
The production plants principally generate metallic waste (54% of
the total quantity of waste produced). These are sold for recycling.
Dangerous waste sorted, which represents 32% of the total quantity
of waste, is removed via authorized channels that abide strictly by
applicable regulations.
2.2.3
I
Taking into account noise and other forms
of pollution specific to an activity
The LISI Group’s sites follow and record all complaints whether
comments, formal or informal, official or not issued by stakeholders.
Thus, 11 complaints were recorded throughout the Group’s sites. The
majority are related to neighborhood disturbances arising from noise
generated by certain of our sites. Each complaint receives a reply
written or otherwise sent to the party concerned.
2.3
I
SUSTAINABLE USE OF RESOURCES
2.3.1
I
Water consumption and water supply according
to local constraints
Water is little used in the manufacturing processes implemented at
the sites. It is mainly involved in parts washing and surface treatment.
However, most process waters are recycled.
All these efforts enable water consumption to be maintained at 1.22 m
3
for €1,000 of added value.
2.3.2
I
The consumption of raw materials and the
measures taken to improve the effectiveness of their use
The LISI Group is very cautious about the consumption of rawmaterials
and works to optimize the use of these resources.
The manufacturing sites primarily use metals, and to a lesser extent
plastics.
Metal work is done mainly by deformation cold forging and hot
stamping causing no loss of material aside from adjustments. More
sites work daily to optimize their material resources (waste reduction,
SMED to reduce losses during adjustment phases, etc.). Finally,
the waste generated by the final stages of production (machining,
sharpening) are sorted and sent for 100% materials recovery.
Corporate social responsibility
6