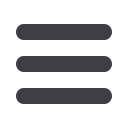
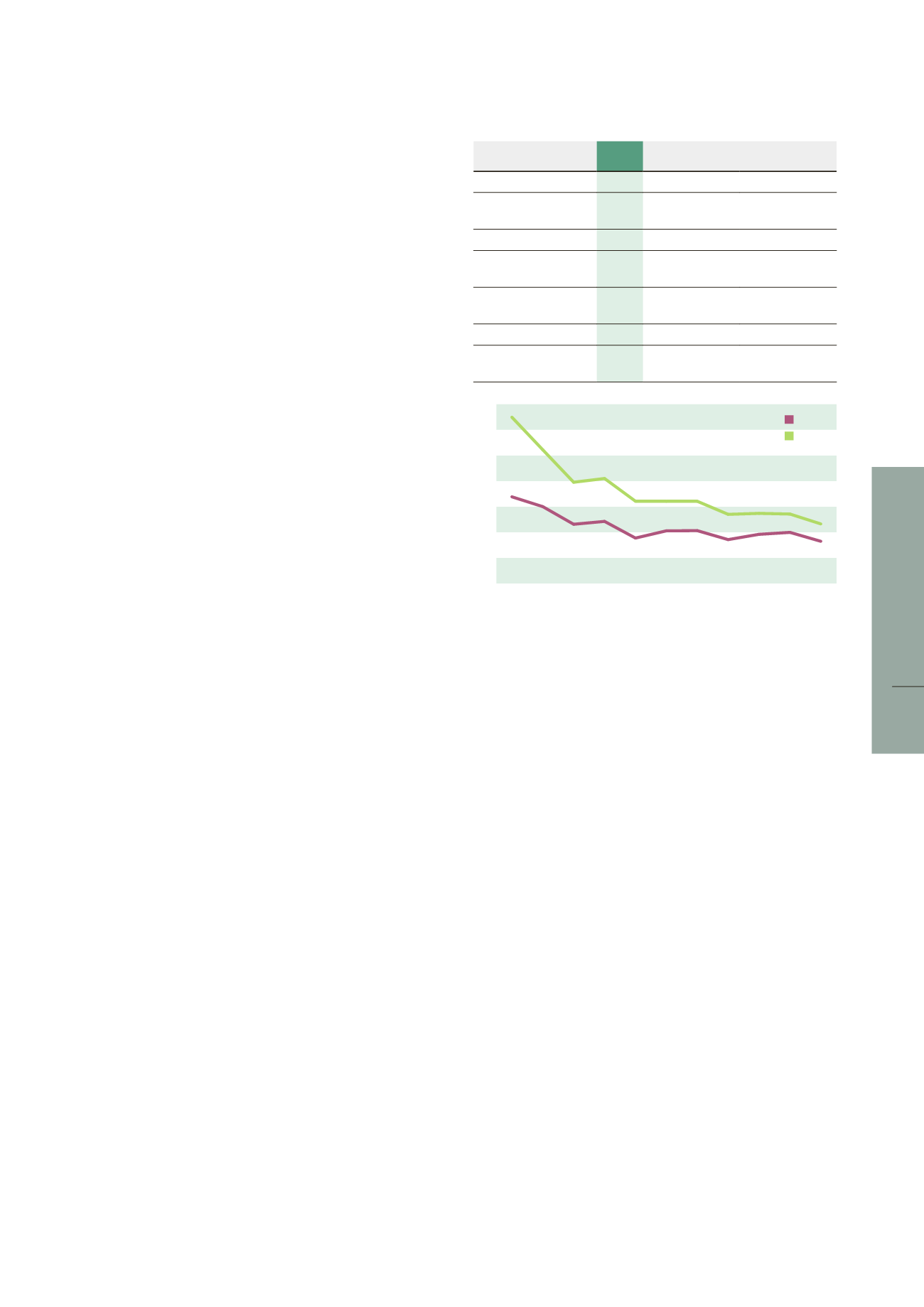
107
CORPORATE SOCIAL RESPONSIBILITY
6
LISI 2017 FINANCIAL REPORT
3.4
|
INTERIM OBJECTIVES FOR 2017
With the objective of meeting the targets set for 2020, LISI had
already defined interim milestones for 2017.
3.4.1
|
Health-Safety:
■■
Each site should achieve a TF1 (number of workplace accidents
with or without lost time for LISI employees and temporary
workers per million of hours worked) of less than ten.
■■
Each workplace accident with or without lost time, for LISI
employees and temporary workers, must be analyzed in a rigorous
manner based on the 8D methodology.
■■
The SCP safety culture program is expected to be launched at each
site, in particular with the training of all managers of the Group.
3.4.2
|
Environment:
■■
each site had to have rolled out an energy consumption reduction
plan;
■■
each site had to have identified its most significant environmental
aspects and defined an action plan to reduce the number of such
impacts.
3.5
|
2017 HSE RESULTS
3.5.1
|
Health Safety
The adoption of a safety culture on a daily basis and the
uncompromising stand in the face of each workplace accident are
paying off.
The results achieved by the Group are very encouraging since
LISI’s performances in 2017 are better than ever. They confirm the
relevance and effectiveness of efforts by all employees and the
Group intends to carry on with them thus proving that accidents are
by no means unavoidable.
To measure its performances, LISI monitors the accident rate of its
employees as well as that of temporary workers working for it.
Thus the accident frequency rate with lost time of LISI employees
(TFO) declined by 56% in ten years to 7.43 accidents per million of
hours worked at end-2017.
The accident frequency rate, with or without lost time (TF1), declined
by 69% in ten years for LISI employees, and by 64% for LISI employees
and temporary workers taken together. This frequency rate is 10.12
accidents with or without lost time per million of hours worked for
LISI employees and 11.61 for LISI employees and temporary workers
taken together. Furthermore, the frequency rate for temporary
workers alone, which reached 25.19 in 2017, has improved by 10% in
five years thanks to the overhaul of their onboarding process.
The severity rate (TG0) , which represents the number of days lost as a
result of workplace accidents per thousand hours worked, remained
at a relatively low level at 0.25 days lost per thousand hours worked.
Indicators
2017
10-year trend
5-year trend
TF0 LISI
7,43
(56%)
(22%)
TF0 LISI + temporary
workers
8,21
(51%)
(20%)
TF1 LISI
10,12
(69%)
(33%)
TF1 Temporary
workers
25,19
(10%)
TF1 LISI + temporary
workers
11,61
(64%)
(28%)
TG0 LISI
0,26
(61%)
19%
TG0 LISI + temporary
workers
0,25
(63%)
10%
TF0
TF1
2007 2008 2009 2010 2011 2012 2013 2014 2015
2017
2016
0
5
10
15
20
25
30
35
Furthermore, because LISI believes that each accident could have
been avoided, a process for the detailed analysis of the causes of
accidents has been implemented to determine the root causes of
workplace accidents, with or without lost time. The objective is to
ensure non recurrence of the most serious incidents. Thus, in 2017,
94% of accidents were analyzed in detail.
As regards production sites, over half (57%) record an accident
frequency rate with or without lost time of less than ten accidents per
million of hours worked.
Furthermore, the results of 55% of LISI’s sites are improving
compared with last year and 12% did not witness any accident in 2017.
It is to be noted that at “Historical sites”, i.e. those owned by the
LISI Group for more than ten years, this improvement is ever more
marked: thus, their frequency rate of TF1 (workplace accidents with
or without lost time) declined by 70% and the gravity rate by 74% in
ten years. This shows that changing the safety culture requires work
over a long period.
Across all of the Group’s production sites, 55 occupational diseases
were reported in 2017.
They relate mainly to joint disorders caused by certain working
gestures and positions. However, all sites are working towards a
reduction of physical constraints through better ergonomic layout of
workstations and by limiting the weight of containers.