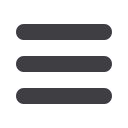

103
LISI 2015 FINANCIAL REPORT
CORPORATE SOCIAL RESPONSIBILITY
In order to ensure and achieve this goal, LISI has adopted
HSE (Health Safety Environment) policy and organization to
identify key areas for improvement, prioritize goals, and derive
the appropriate actions. This policy and this organization are
based on the international OHSAS 18001 standard (international
standard governing the management system of health and
safety at work).
In order to provide itself with the resources to succeed in this
field, each production plant as at least one HSE Leader whose
role is to lead the HSE activity for his plant and is the guarantor
for the implementation of an HSE management system.
In addition, the LISI Group has an HSE Steering Committee
whose role is to analyze accidents and major incidents within
the Group and to establish HSE strategies aimed at reducing
risks related to work, the environment and loss of goods. The
Committee is chaired by the Chairman and CEO of the LISI
Group and the Director of Manufacturing and Procurement. It
comprises the HSEManagers from each division, the LISI Group
HSE Manager (who leads it) and the insurance broker working
on behalf of the LISI Group.
In terms of Safety, acceptance and dedication of each employee
of the Group are actively sought in the process of improving the
safety of our sites.
OnMay6, 2014anHSEForumbrought together themanagement
of each division, all the Site Directors and the HSE Managers
and the LISI Group; they have set for themselves ambitious
goals. In particular:
■■
in terms of safety: at the end of 2016, all the sites of the
LISI Group will be obliged to display the frequency rate of
workplace accidents, with and without work stoppage (TF1)
of less than ten days, and this incorporating the temporary
employees working on behalf of the Company;
■■
in terms of environment: each of the three divisions of the
LISI Group must reduce its industrial impact by reducing its
consumption of energy by 10% in comparison with the 2014
figures;
■■
in terms of HSE: the LISI Group is seeking to embed a
company HSE culture. These objectives will be achieved via
the implementation of an HSE Excellence program and a
Safety Culture program.
A new HSE Forum will take place in 2017 to report on the
achievement of these objectives to all the plant managers and
HSE managers.
The General Management of LISI has undertaken to put in place
an ambitious program aimed at achieving industrial excellence
in the field of HSE. This program is aimed at:
■■
setting a common course;
■■
initiating a federating and structuring project;
■■
deploying the resources to achieve our objectives;
■■
utilizing the best practices existing within the Group.
LISI defines HSE Excellence as the fact:
■■
of having robust foundations: in other words being
irreproachable in the field of HSE, complying with applicable
regulations, being a champion in certifications;
■■
of having the best practices in HSE management, leadership
in the field, resolution of problems and control of risks;
■■
of setting ambitious objectives in terms of health, safety and
the environment.
This is the reason why LISI has launched this program of which
the clear objective is to make available to each plant tools
for leadership and assistance to enable them to achieve HSE
Excellence.
Furthermore,
technically
, LISI is constantlyworking to improve
its workstations. Thus, in 2015, LISI invested €6.8 million in the
field of safety and the environment, including for the safety
of its machinery and for the implementation of ergonomic
facilities and assistance in handling.
Then, froman
organizational
point of view, the sites implement
a health and safety management system that is compliant with
the international standard OHSAS 18001. Furthermore, all the
industrial sites (excluding the recently acquired Manoir sites)
have been certified to this same standard by an independent
external organization.
But it is from the
behavioral
standpoint that the LISI Group
has chosen to put forth the greatest efforts. The point here is
mainly to give security the place it deserves: it should be the
primary concern at the heart of workshops, since this is where
the vast majority of accidents occur. This is materialized by the
fact that Safety is the first issue dealt with during the daily PSM
rituals (Problem Solving Management) at each level of plant
management (Autonomous Production Group – Autonomous
Production Unit – Site).
In addition, in 2015, LISI began the implementation of a Safety
Culture program, which must:
■■
deal with behavior-based causes of workplace accidents;
■■
enable the management (from the plant manager to the shift
supervisors) to understand the behaviors and give them the
levers to act against them;
■■
develop a Safety Culture within the teams through the
deployment of a structured communication campaign.
This long-term program is starting to bear fruit on the sites
which have started its deployment.
Each employee, whether operator or manager, builds this
safety culture. Everyone should participate in creating a work
environment where risk is under control. And each employee
must also pay attention to their own safety as well as that of
their colleagues.