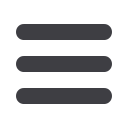
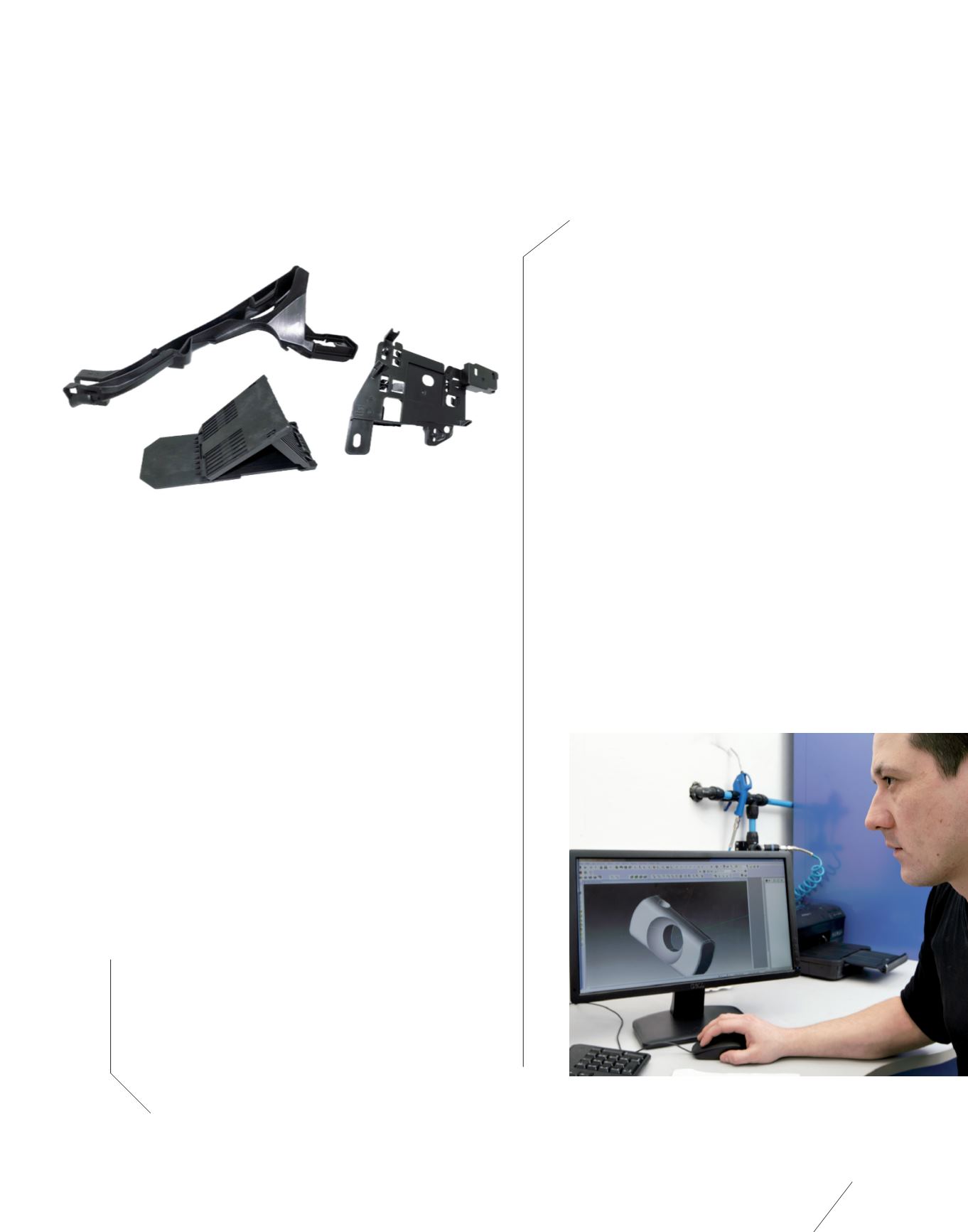
33
LISI 2015
Between
6
and
7
kg
This is the weight of chassis screws’
for 1.4 metric ton vehicle
M E D I C A
L
3D PROTOTYPES
TO EASE
OSTEOINTEGRATION
LISI MEDICAL is a stakeholder for the discussions
held within the group on additive manufacturing
using 3D printing system. These new technologies
allow to manufacture implants with integrated
porous surfaces mandatory to facilitate the
structural and functional connection with the bone
(osteointegration). So with additive manufacturing,
implants aremanufactured directly in one operation
without additional coating currently obtained
by expensive techniques. The first prototypes of
cups, offered with various external porosities, were
produced in 2015. The development shall continue in
2016 in order to assess the opportunity to offer this
type of industrial solution to all of our customers.
A U T O M O T I V E
LIGHTER
CLIPPED SOLUTIONS
The teams of the Clipped Solutions Business Group have managed
to develop and market simplifications solutions for assemblies
and lighter vehicles. These innovations have helped replace steel
with high performance plastics materials for some parts. The first
series applications (wheel chock, hand brake cable guide), have
already been introduced on the market. They contribute to up to
500 grams weight reduction for each vehicle. In collaboration with
the manufacturers, the approach is already pushed further with
analysis carried out on new vehicles, in service and during their
assembly. These discussions allow the LISI AUTOMOTIVE teams to
further optimize these proposals through new simulation tools,
which enable quick delivery of prototypes and of preproduction
parts printed in 3D.
LISI MEDICAL Fasteners Neyron