
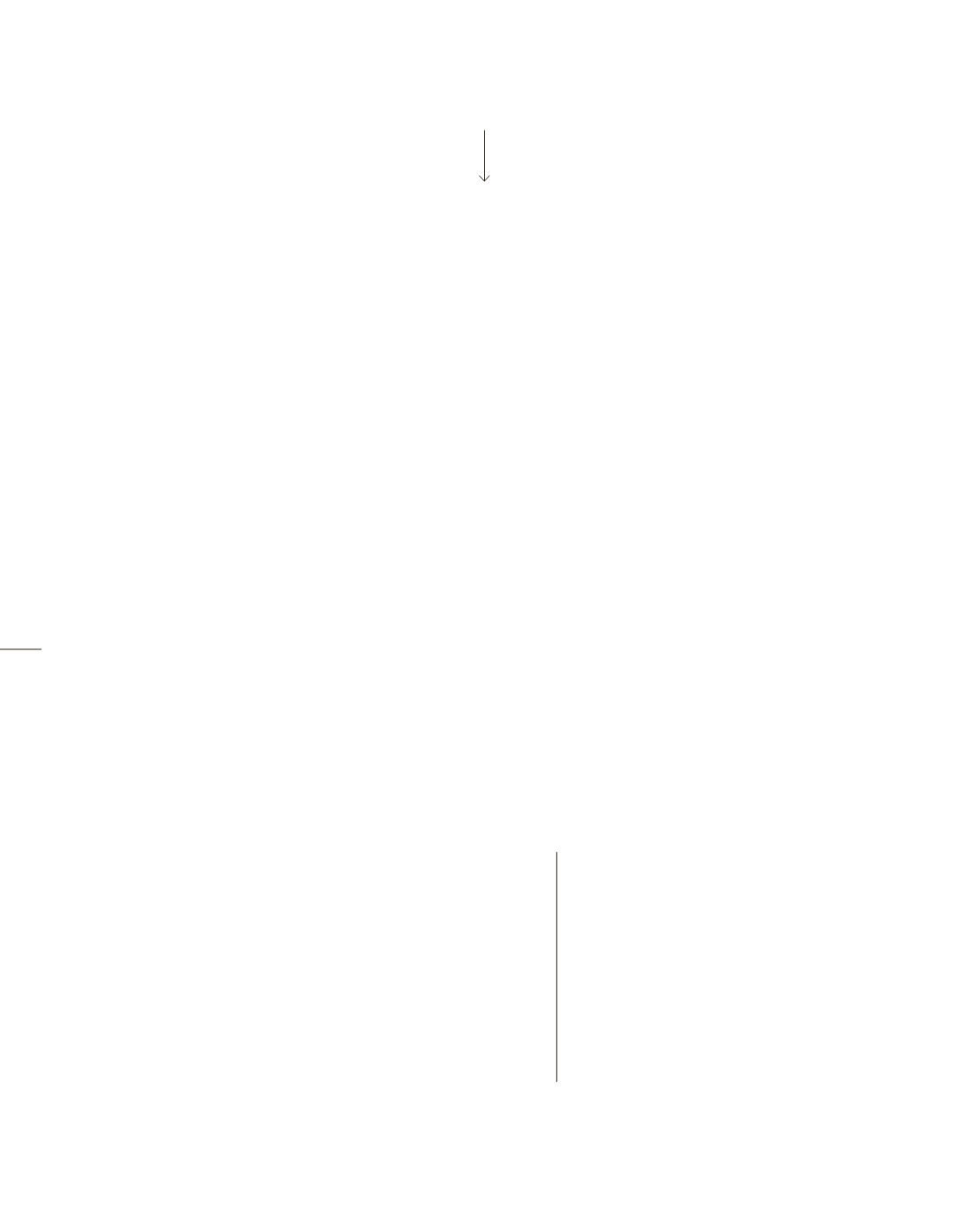
Thehealth andprotectionof employees, aswell as thepromotion
of quality of life at work, have always been a priority for the LISI
Group. The implementation of continuous improvement
programs on these topics, with specific objectives, is the
keystone of LISI management’s action plan to improve accident
prevention across the Group’s divisions. The target set for 2020
to lower the accident rate below the threshold of 8 per million
hours worked for each site in the Group is on track.
Accidents in sharp decline
The implementation of the SCP program (
Safety Culture
Program
) has enabled the Group to achieve the best results
ever recorded in its history in terms of safety. Measured on
December 31, 2017, the frequency rate of accidents with or
without a work stoppage involving a LISI employee or a
temporary worker (TF1) reached 11.61, down 27% in 5 years
(-64% over 10 years). The lost time accident rate (TF0) fell by
19% over 5 years. In total, 55% of LISI sites show improved
results compared to the previous year; 57%of themhave a TF1
of less than 10, this threshold being the intermediate target
set by LISI management for 2017. The historic sites, owned by
the Group for more than 10 years, show even greater progress.
A common prudential approach
Developed in the framework of LISI E-HSE (
see also page 62
),
the deployment of the SCP program has made it possible to
accelerate the sharing of effective precautionary behaviors
and the adoption of a common risk prevention culture. These
indispensable steps form the basis of this progress initiative.
HEALTH & SAFETY
PROTECTION AT
WORK AIMING HIGH
-19
%
DECLINE IN TF0 ACCIDENTS
(WITH STOPPAGE) SINCE 2012
(EMPLOYEES + TEMPS)
-27
%
DECLINE IN TF1 ACCIDENTS
(WITH AND WITHOUT STOPPAGE)
SINCE 2012 (TEMPORARY EMPLOYEES)
“Health and safety issues are one of the keys
to improving the Group’s performance results.”
64
CORPORATE AND ENVIRONMENTAL RESPONSIBILITY