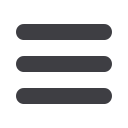
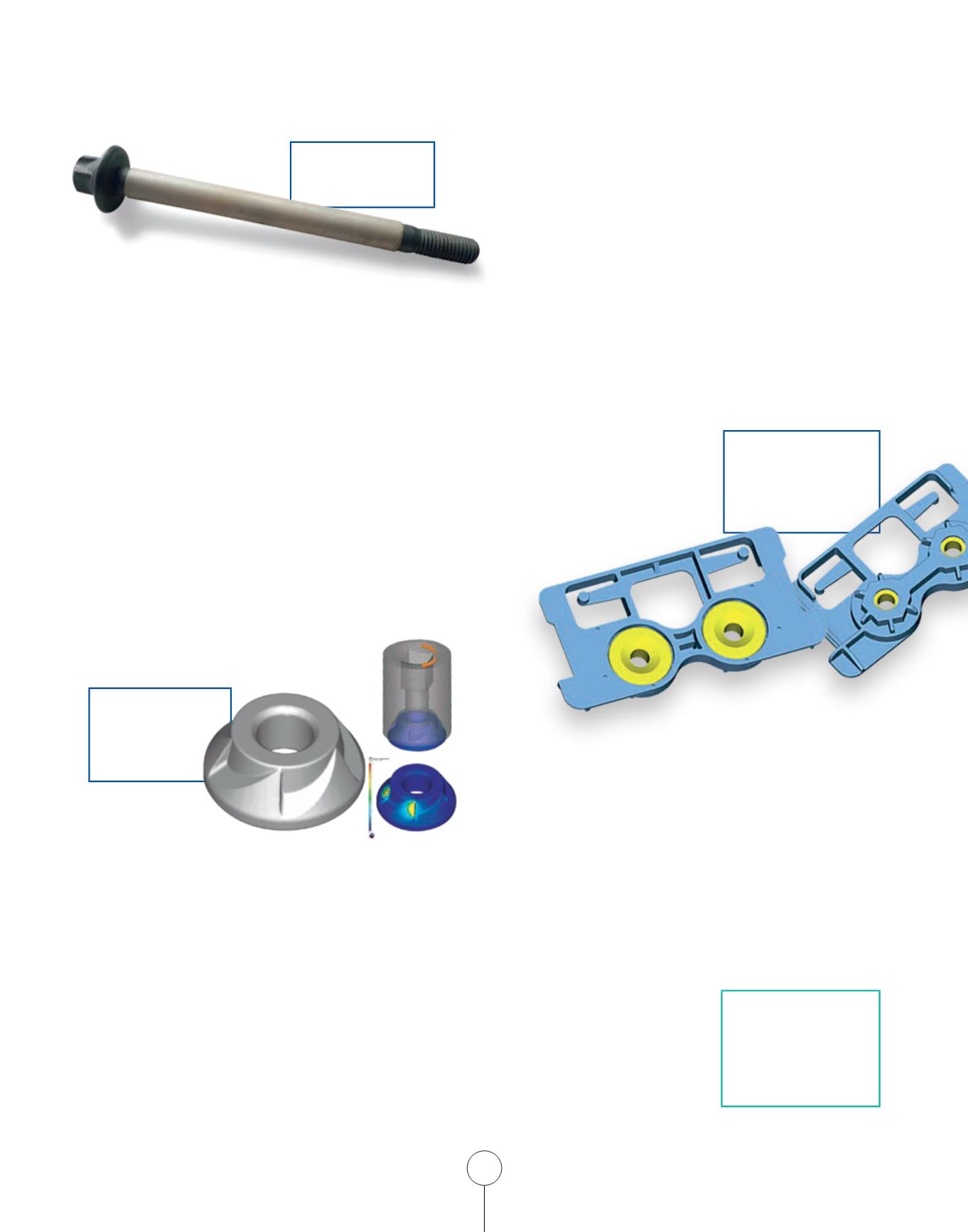
ELECTRICAL
insulation, high
mechanical resistance
LISI AUTOMOTIVE
INSULATING SCREW
EQUIPPING HYBRID
VEHICLES
The rapid development of hybrid and fully electric vehicles
generatesnewconstraints in termsof fasteners. Theassembly
of organs operating at different electrical potentials, made
necessary to optimize the space in the vehicle, is one of these
new issues. To meet those requirements, LISI AUTOMOTIVE
hasdevelopeda longM7 (100mm), class 10.9screw, insulatedon
the non-threaded part by thermoplastic overmolding. Various
laboratory tests have qualified the electrical resistance of
the insulating protection (breakdown potential) as well as its
resistance to corrosion in various environments.
LISI MEDICAL
PROTOTYPING
GAINING AGILITY
This year LISI MEDICAL developed a new rapid prototyping
cell at its Neyron site. Consisting of a milling center, a
turning-milling center and a lathe, the unit optimizes the
industrialization of mass production parts, reserves a
non-production area for developments and debugging, and
accelerates qualification processes. It offers the ability to
produce low volumes without
disturbing the “high-runners” and
allows the site to gain agility.
LISI AUTOMOTIVE
METALLOPLASTIC
SOLUTIONS
LIGHTER VEHICLES
Capitalizingon itsdual expertise in low-alloy steel cold-heading
and plastic injection technologies, LISI AUTOMOTIVE offers
metalloplastic solutions that lighten automotive vehicles and
contribute to the reduction of greenhouse gas emissionswhile
reducingproductioncosts. Thedesignof the injectedpartof the
newdoor latches allows for seamless installation. This system,
which maintains the mechanical robustness of the function,
reduces the assembly time at the manufacturers and offers
aweight reduction of 50%compared to an all-metal solution.
LISI AUTOMOTIVE
TAMPER-PROOF NUT
INCREASING SECURITY
I n o r de r to mee t t he demand o f manu f ac t u r e r s ,
LISI AUTOMOTIVE has developed a nut whose geometry and
mechanical properties make it easy to screw but impossible
to unscrew quickly without the right tool. The design and
characteristics of this tamper-resistant nut, which enhances
the safety of the vehicle interior, have been validated by
digital simulation. An initial version of the nut, proposed in
low alloy steel with M6 tapping, is now available and can be
offered in various diameters. A tamper-proof screw version,
based on the same principle, is under development.
3915%
This is the production
time devoted to
development and
industrialization projects
absorbed by this newunit
SECURING
sensitive elements
of the vehicle
cabin and ease of
implementation
50%
weight gain
compared to “all metal”
solutions +mechanical
robustness and time saving
during assembly