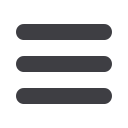
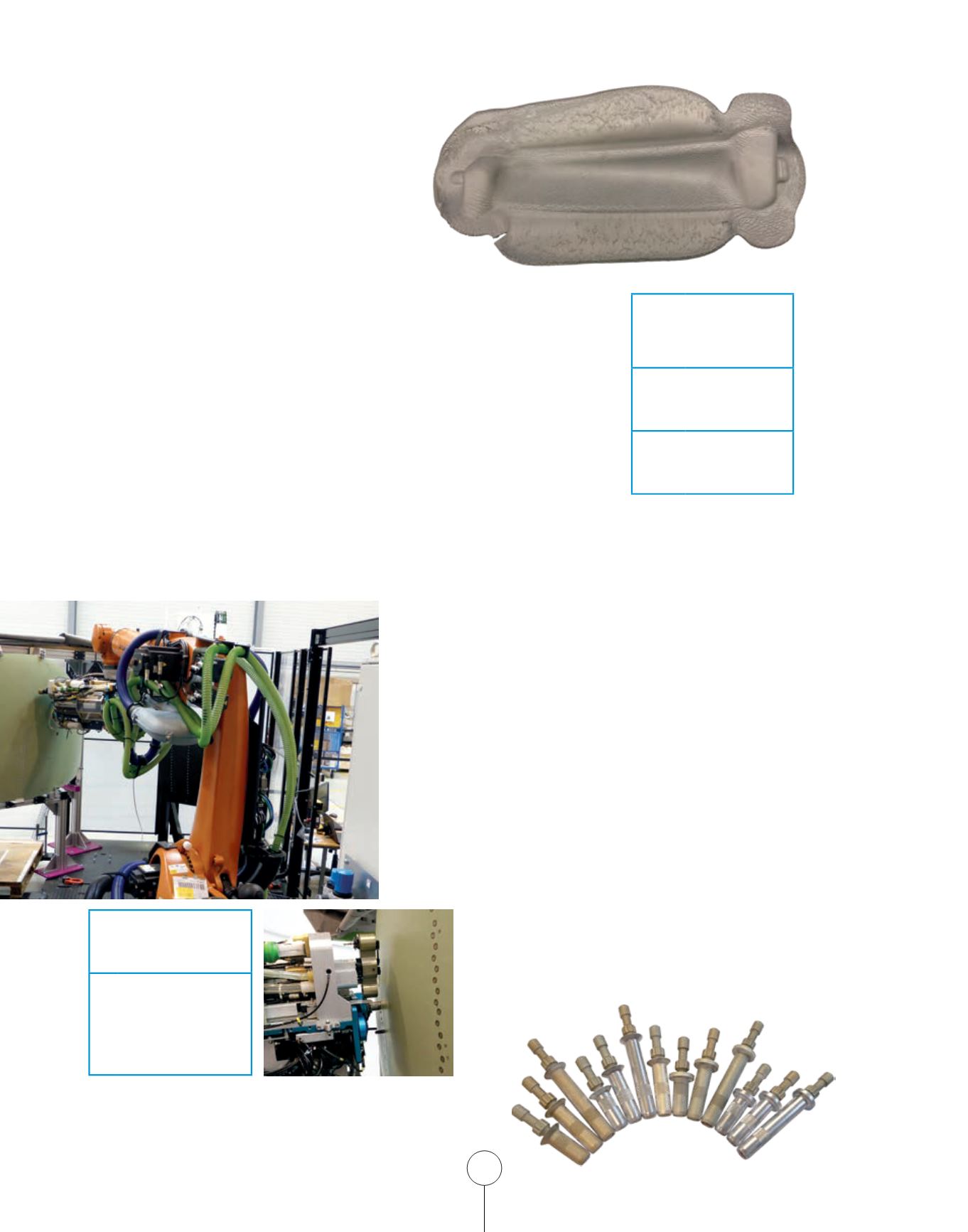
I
PRODUCTS
LISI AEROSPACE
TiAl
FORGING THE MOST
COMPLEX MATERIALS
TiAl (Titanium-Aluminum alloy) is an intermetallic, lightweight material that can
withstand high temperatures. It gradually replaces the Nickel-based superalloys
used in the hot parts of engines, such as turbine blades, while weighing only
half as much. Very difficult to deform because of its low ductility, its industrial
processing is very complex. To circumvent this obstacle, LISI AEROSPACE has
developed an alternative so-called “hot dies” forging technology at its Forges de
Bologne plant. It maintains the productivity of conventional forgingwhile achieving
a metallurgical quality close to that of isothermal forgings (forging installation
operating at 1,250/1,300°C), particularly in terms of microstructure homogeneity
and external health of the parts. By reducing production costs to levels acceptable
by the market, this innovation will promote the rise of this exceptional material on
new generation engines.
LISI AEROSPACE
ROBOID PROJECT
VALIDATING THE TECHNOLOGIES
OF THE FUTURE
To improve competitiveness and ensure high production rates, aircraft
manufacturers are now focusing their efforts on the automation and
efficiency of assembly processes. Since 2011, LISI AEROSPACEhas initiated
the development of automated structural assembly technologies through
the LISI@OneSide program. On this basis, in collaboration with Dassault
Aviation, which contributes its expertise as aircraft manufacturer, and
thanks to the support of the General Directorate of Civil Aviation (DGAC), we
have built the ROBOID collaborative project. This industrial demonstration
project aims to demonstrate the relevance of the LISI@OneSide automated
assembly system with the new OPTIBLIND ™ blind fasteners and CLY62
temporary fasteners. Implemented in an environment that
is representative of actual production conditions, ROBOID
proves the robustness and economic benefits of this assembly
technology and validates this major technological leap in aircraft
production.
1
proven automated
assembly solution from
one side of the structure
100%
robotic sequences
(drilling, sealant
application, assembly
and control)
36-20Kg
on an engine thanks to
TiAl turbine blades
X
4
Productivity gain
over isothermal
forge
X
2
Static strength
of forgedTiAl vs.
moldedTiAl