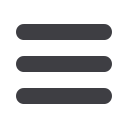
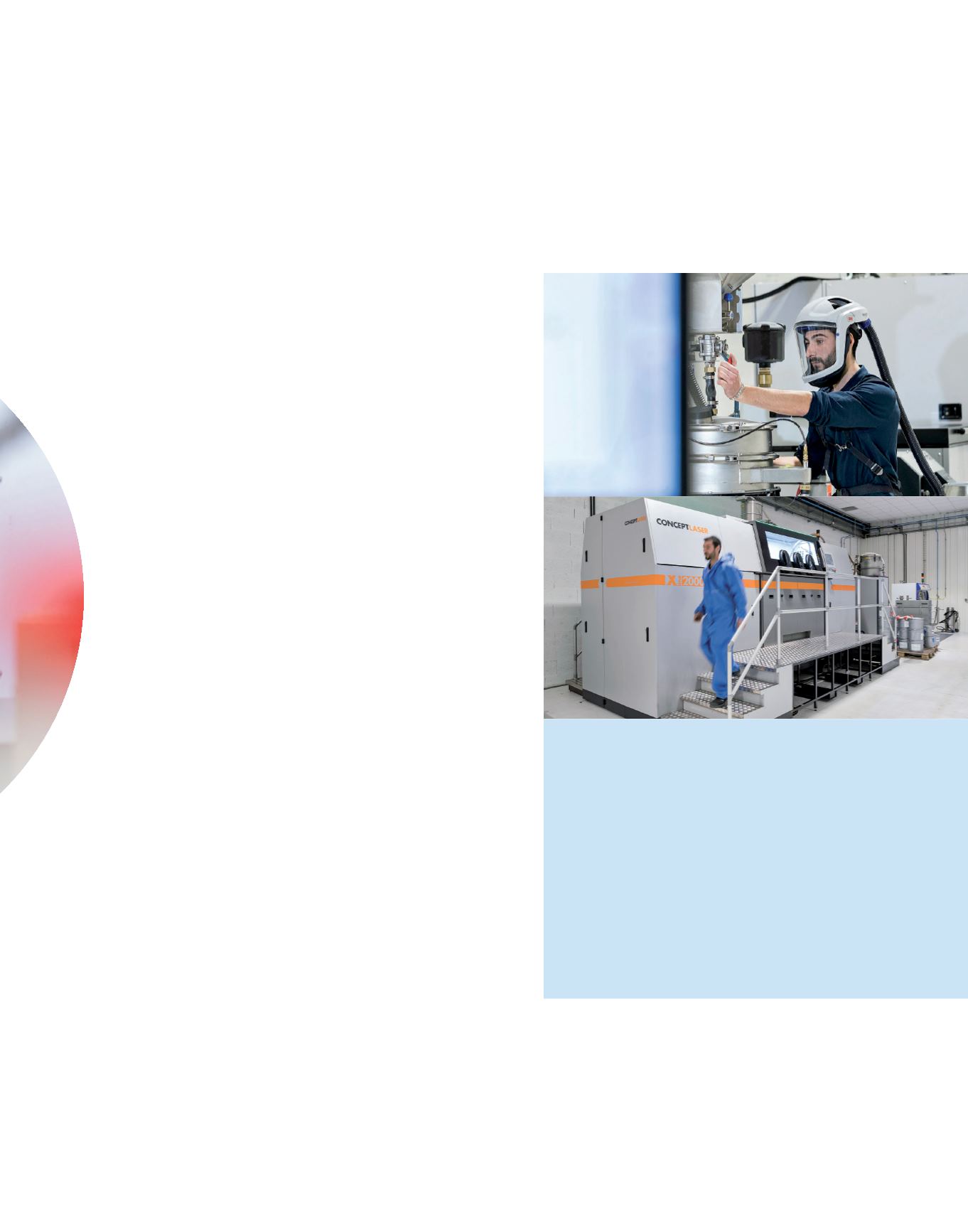
LISI 2016 ANNUAL REPORT
I
17
LISI AEROSPACE Additive Manufacturing
SUPPORT OFFER
• Component Co-Design in Additive Manufacturing
• Topology optimization
• Settings definition (new materials and processes)
TECHNOLOGIES
• Laser Beam Melting – LBM
• Electron Beam Melting – EBM
MATERIALS & RAW MATERIALS
• Metals: Titanium, Aluminum, Inconel, Super Alloy
• Plastics: 2210FR, 2241FR, 2200, Ultem1010, Ultem9285
3
D is on. By opening up to the methods of additive
production, LISI AEROSPACE intends to play a
leading role in this major technological evolution.
In the heart of the vineyards of Graves, near
Bordeaux, the experience has taken shape, with
LISI AEROSPACE Additive Manufacturing (LAAM)
settling its premises on 1,800 m
2
. This subsidiary 60% owned by
LISI AEROSPACE and 40% by Poly-Shape, a pioneer of additive
metal manufacturing since 2007, has positioned itself to meet all
the expectations of the aviation industry.
A new industrial culture
“The opportunities are many,
says Jean-Louis Colders, CEO of
LISI AEROSPACE.
Standards must be developed and we must be
involved in this movement that will drive a new industrial culture.
The new lighter hollow parts with complex shapes cannot be
manufactured with conventional methods. Additive manufacturing
can produce them with levels of quality and strength consistent
with the requirements of the aerospace industries.“
Components co-design
With a team of 18 people, most of them from staff of both
partners, LAAM has the skills and the means of production
necessary to operate the main 3D technologies available –
laser beam melting and electron beam melting of – to provide
the aerospace market with components designed for additive
manufacturing on an industrial scale. LAAM’s offer covers
technical support (help with product design, change in shape
to facilitate additive manufacturing, topological optimization),
process control (manufacturing simulation, materials sizing,
control and characterization of powders, etc.) and processes
(finishing and controls). Large machines have been completing
this system since February 2017.
Combining technologies
In addition to the controls built into the manufacturing process
itself, LAAM has a mechanical testing laboratory and upstream
to that, a powder testing laboratory (composition, distribution,
granulometry, etc.). The company is also working on the
combination of additive and conventional technologies (extrusion,
molding, forging, etc.). LAAM has taken steps to obtain the
accreditations from its main customers (Airbus, Safran, Dassault
Aviation, Thales Alenia Space and Euro Heat Pipes).