
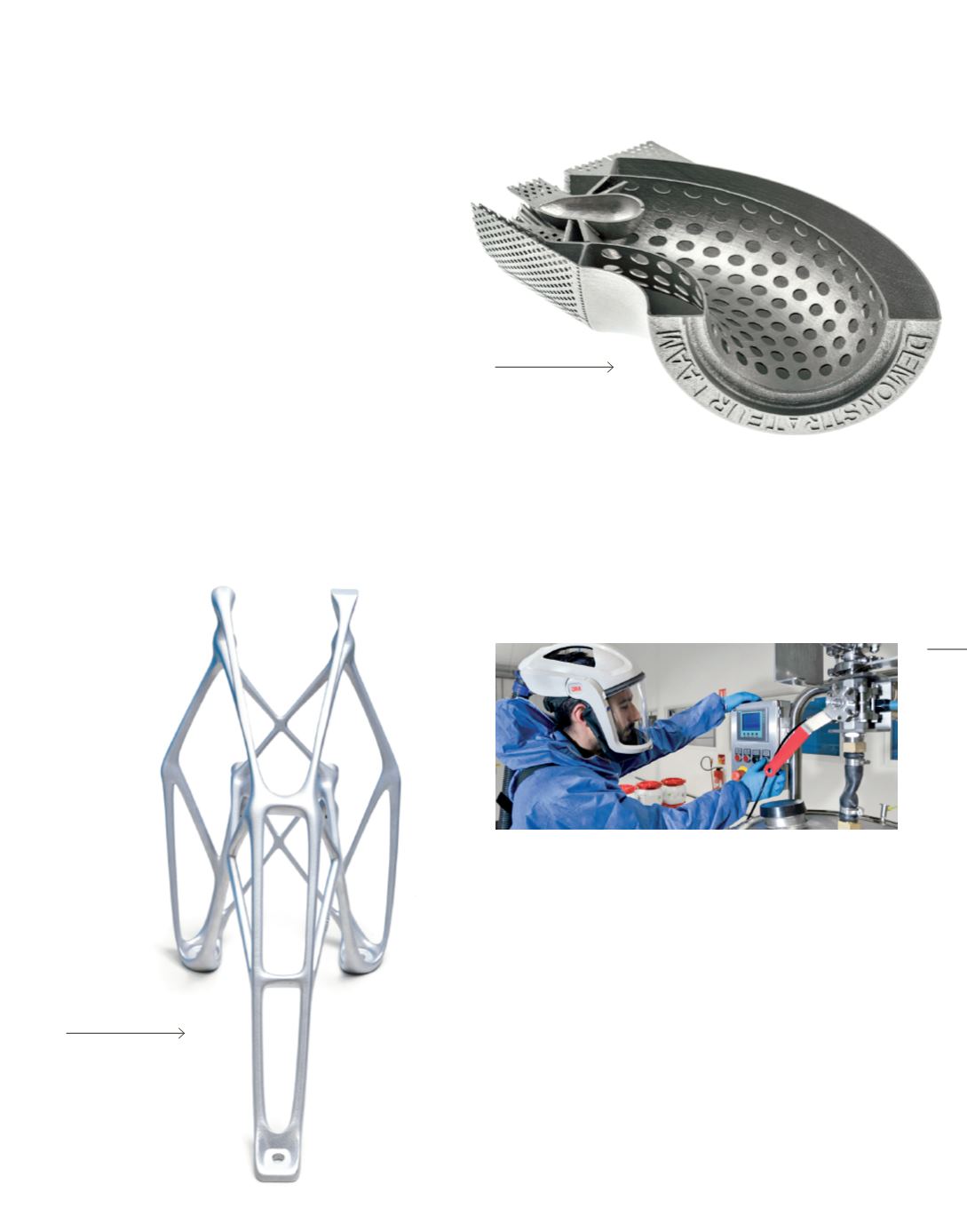
First parts in flight!
The close collaboration between LISI AEROSPACE’s customers’
research depar tments and LISI AEROSPACE Additive
Manufacturing’s engineers has already made it possible to
manufacture products suitable for additive manufacturing,
such as the water separator in use on Falcon 2000, or the
antenna support in use on the KOREASAT-7 satellite launched
from the Kourou launch pad on May 5, 2017.
Positioned from the outset to meet the expectations of the
aeronautics, defense and space industries, LAAM is able to
help design products made in 3D (shape modification,
topological optimization, re-design, etc.), to produce complex
additive manufacturing processes while mastering all
post-processing aspects (finish and checks).
ADDITIVE MANUFACTURING
LISI LEADER OF 3D METAL PRINTING
R
elying on LISI AEROSPACE Additive Manufacturing’s
(LAAM) know-how, the LISI Group is strengthening its
expertise in 3D Metal printing technologies. During
the year 2017 LISI AEROSPACE Additive Manufacturing
structured its teams and strengthened its workingmethods
so as to apply the requirements of industrial processes to
3D printing. The goal: to achieve the required levels of
requirements in the aeronautical markets in technical and
economic terms. The efforts put forth made it possible to
market the first series of products and parts qualified for
aeronautics, in use on several aircrafts.
Exploded view of
a water separator mounted
on FALCON 2000.
Antenna hub in use on
the KOREASAT-7 satellite.
27
INNOVATION